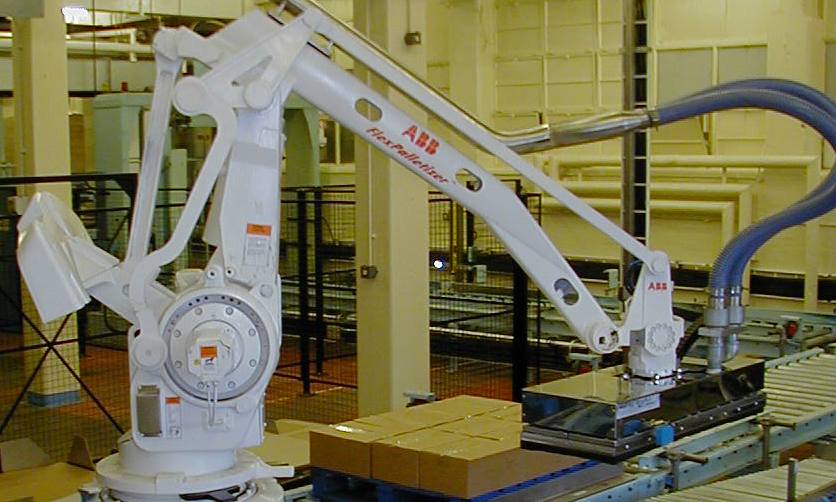
Problem presented:
The existing conventional layer palletiser had become obsolete and was no longer supported. Additionally it was in very poor condition and causing significant downtime with a labour intensive manual changeover between products. The product feed came from a packaging plant four stories above in a steel and concrete frame building.
Analysis undertaken:
- Product range and throughput.
- Pallet stacking and interleaving requirement.
- Construction work and fire zone compartmentalisation.
- Method and cost of implementation.
Suggested solution:
4 axis palletizing robot with multizone head using bespoke vacuum gripper and side channel blower. Product feed via decline modular conveyor with mechanical fire hoods between floors. Auto reject of incorrectly picked product. Unmanned machinery hence remote alarm SMS to operator in a number of production zones.
Implementation and benefit:
Project managed by Epsilon Engineering using a mixture of customers approved suppliers and introducing contractors with specialist skills where required. Design of bespoke items by Epsilon Engineering. Significant saving to customer over conventional fixed price contract. Project completed to time and cost providing a very robust & durable solution with a long MTBF.